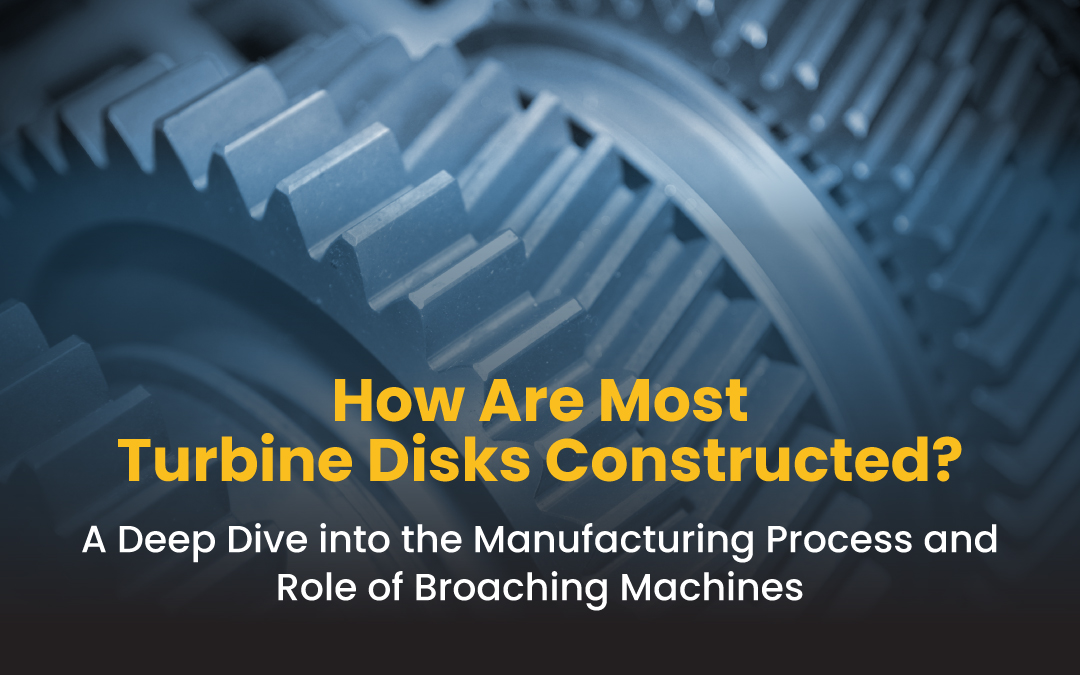
Turbine disks are the most important element in current aerospace and power generation systems. It is the central hub for the turbine blades and converts thermal energy into mechanical energy. Such turbine disks are part of a very complex manufacturing process that demands high-precision engineering to provide reliable and efficient performance at extreme operating conditions. From the selection of materials to the fine art of machining, every step in manufacturing shall have very strict safety and efficiency standards. Among these, first and foremost, will be the broaching machine, which is one of the important tools in achieving the geometric specifications and very-smooth surface finishes required for turbine disks.
The manufacture of turbine disks involves a process that combines advanced machining techniques with the principles of materials science. These disks are made using high-strength alloys that can withstand the extreme temperatures and pressures inside a turbine engine. Nickel-based superalloys are typically used, as they maintain structural integrity even at very high temperatures. Broaching machines are renowned for their precise mastery of the broaching technique. Equipment provided by companies like Taizhou Chengchun Automation Equipment Co., Ltd. plays a crucial role in the precise shaping process of these critical components.
Material Selection and Initial Shaping
The process begins with the selection of the material to be used. Turbine Disks undergo intense stresses, especially in aerospace applications, on account of intense heat, centrifugal forces, and mechanical strains. Superalloys, mainly based on nickel and cobalt, find applications due to their high stability at raised temperatures, coupled with resistance to oxidation and corrosion.
Once the material has been selected, it is then shaped into a crude disk through forging or casting. Due to the fact that forging produces a strong and dense structure, it is preferred for the disk of the turbine as its structures have high stresses during service. After that, heat treatment is given to the disk so that its mechanical properties would be developed without any strength deficiencies during service.
Now, in order to do this, accurate machines have to be made. Their function is to remove material precisely, hence helping shape the smallest details for the disk, besides allowing holes, slots, and grooves-all essential to assembly and operation.
Precision Machining: The Role of Broaching Machines
Precision machining follows once the general shape of the turbine disk has been roughly machined. At this stage, it will be critical to ensure that a tight tolerance required for the disk at the end can be achieved. It is for this reason that broaching machines are useful for this stage because they can cut the material relatively quickly and accurately, both for high accuracy and surface finishes.
A broach is a cutting tool that employs a number of cutting teeth. The tool could either be withdrawn through or advanced through the workpiece. In that way, this becomes an extremely closely controlled material removal process. It is better suited to making complex shapes and features where there are very rigid dimensional tolerances. Often, there will also be secondary features such as keys or splines, but really exotic geometries are often required in the case of turbine disks.
Precision machines stand out in this application because they add advanced automation to such machines. These machines shall deliver fast production with exceptional precision, hence ensuring that every turbine disk is made with unshaken quality. Their ability to attain close tolerances reduces the chances of defects, hence ensuring the final product shall pass such testing conditions required for the hostile environments in which the turbine disks operate.
Surface Finishing and Quality Control
Once the basic geometry of the turbine disk is attained, the next stage involves surface finishing and testing. Turbine disks should possess a surface finish on the smoothest possible scales since this will reduce friction and wear that are crucial in their longevity and reliability. In addition, the surfaces must pass strict quality requirements since failure possibilities via fatigue or stress cracking arise quite often from cracking fracture while the turbine disk is in operation.
Very critical to the attainment of required surface finishes, the broaching machines shape the turbine disk into very precise dimensions and also enhance the texture of the finishing to meet the specifications in industries. This is very important in aerospace and power generation where minute defects may cause complete failure.
At this stage, turbine disks are subjected to very stringent scrutiny to ensure their conformity to all design specifications. All dimensions of such a critical feature are stringently cross-checked to be error-free, with material properties tested for any sign of absence of integrity in the disk itself. Machines for broaching minimize the likelihood of defects because this technique has a controlled manner of material removal.
Integrating Broaching Machines with Other Technologies
Although broaching is an important process, it may play a supportive role in manufacturing processes to achieve the needed end product. For example: use of CNC machines for fine finishing and intricate features, as well as where EDM can be used to have a higher degree of accuracy for cuts or holes that may be needed. Such technologies are usually allied to a fully automated production system that is perceived to raise the speed of production while improving the consistency of the turbine disks.
Included in the range of this high-tech machining product are the easy-to-synchronize broaching machines with systems such as CNC and many other technologies, thereby allowing greater flexibility and an efficiency increase in the production process-an attribute indispensable in today's manufacturing environment-that results in faster and more efficient production lines, capable of taking on the challenging demands posed by industries such as the aerospace sector, where the quality and reliability of components assume a gigantic role.
Final Testing and Certification
After finishing and main assembly machining, the turbine disks undergo a final testing process for absolute performance and safety tests. This ultimate assessment includes stress testing, fatigue analysis, and thermal cycling. The aim of such tests is basically to simulate extreme situations that the disks will experience when in operation. From such tests, only awarded certification is given to the disks for possible use within critical systems.
Generally, turbine disks are to be required precision tools, but most importantly relate to broaching machines. As such, besides achieving the needful geometrical accuracy, such machines facilitate better efficiency in a production cycle. By minimizing waste in material, it also permits high-speed production of parts with better surface finishes. It is, therefore, the greatest power to be given to manufacturers to combat stringent demands of industries like aerospace and power generation.
Conclusion
Manufacturing of turbine disks is the highly specialized and technical process calling for accuracy right from beginning to end. From the selection of suitable materials or shaping them at the first stage, machining at last stages until surface finishing, each step in the manufacturing process matters for ensuring that turbine disks work efficiently in demanding conditions. Some of the most critical machines that achieve this are the broaching machines, one of which is Taizhou Chengchun Automation Equipment Co., Ltd. They provide precision and speed, just like most industries need, such as aerospace and power generation. With modern manufacturing technologies like broaching, companies can produce more efficiency while maintaining the quality and strength of these crucial parts.
Share this post
Leave a comment
All comments are moderated. Spammy and bot submitted comments are deleted. Please submit the comments that are helpful to others, and we'll approve your comments. A comment that includes outbound link will only be approved if the content is relevant to the topic, and has some value to our readers.
Comments (0)
No comment