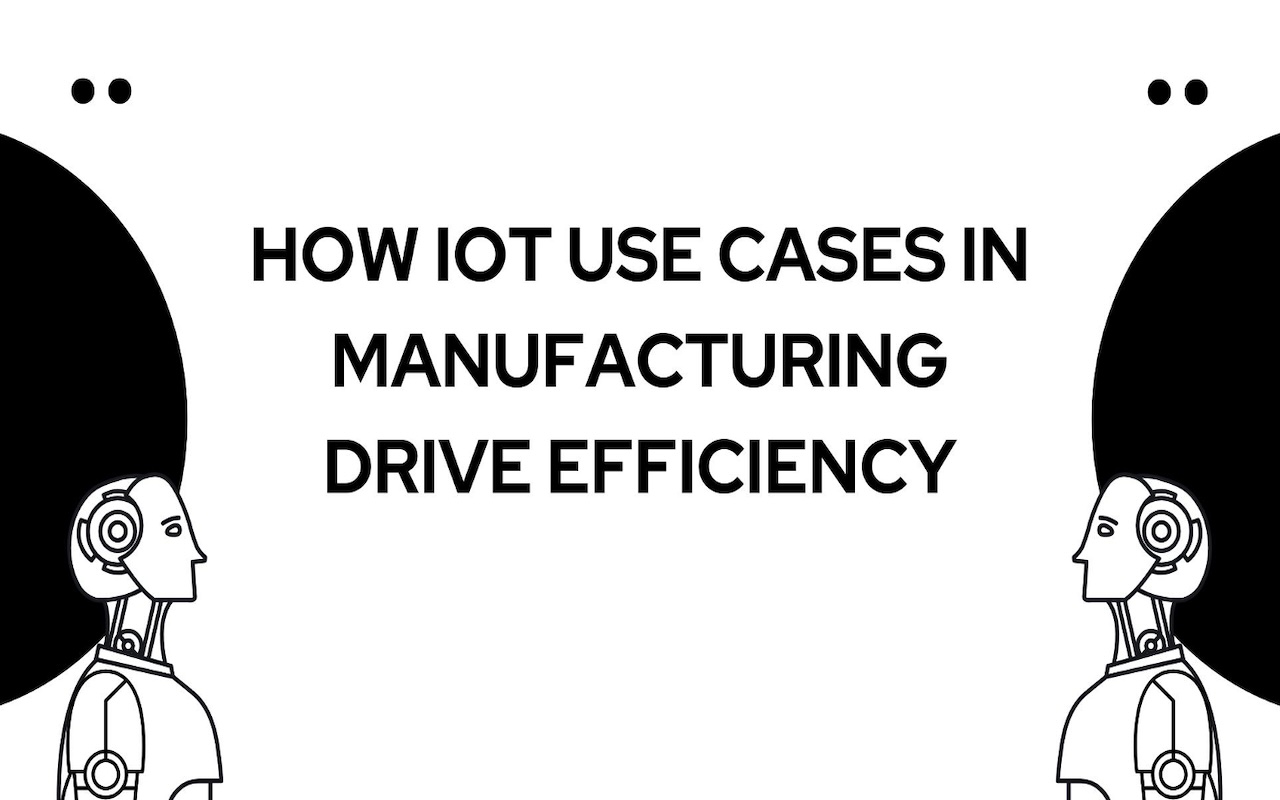
Imagine stepping onto a factory floor where machines communicate seamlessly, alerting operators before issues arise, and production lines adjust in real-time to meet demand. This isn't a glimpse into the distant future—it's the present reality in smart manufacturing, thanks to the Internet of Things (IoT).
How IoT is revolutionizing manufacturing and driving efficiency to new heights.
1. Predictive Maintenance: Anticipating Issues Before They Arise
Think about the inconvenience of a car breaking down unexpectedly. Now, magnify that to a manufacturing setting where a single machine failure can halt an entire production line. IoT enables predictive maintenance by embedding sensors into machinery to monitor real-time performance metrics such as vibration, temperature, and energy consumption.
These sensors detect anomalies, signaling potential issues before they escalate into costly breakdowns. For example, an IoT-enabled factory reduced machine downtime by 22% through predictive maintenance, saving thousands in operational costs.
2. Quality Control: Enhancing Product Consistency
Consistency is crucial in manufacturing. IoT plays a pivotal role in quality control by collecting data throughout the production process. Sensors monitor variables like temperature, humidity, and pressure, ensuring they remain within optimal ranges.
If deviations occur, the system alerts operators to take corrective action promptly. This proactive approach minimizes defects and ensures that customers receive products that meet high-quality standards, reducing waste and improving overall efficiency.
3. Inventory Management: Streamlining Supply Chains
Managing inventory levels can often feel like a balancing act. Too much stock ties up capital, while too little can halt production. IoT streamlines inventory management by using RFID tags and sensors to track raw materials and finished products in real-time.
This real-time visibility enables manufacturers to:
- Optimise stock levels, reducing waste
- Automate reordering processes to prevent shortages
- Improve warehouse management for faster shipping
By eliminating inefficiencies, manufacturers can reduce costs while ensuring production lines run without unnecessary interruptions.
4. Energy Efficiency: Optimizing Resource Consumption
Energy costs can be a significant burden for manufacturers. IoT contributes to energy efficiency by monitoring and managing energy consumption across facilities.
- Smart meters track energy usage patterns
- Automated systems adjust power consumption based on demand
- AI-driven analytics recommend strategies to reduce energy waste
For instance, manufacturers using IoT-driven energy management have reduced electricity consumption by up to 18%, leading to both cost savings and a lower carbon footprint.
5. Worker Safety: Prioritizing Employee Well-being
A safe workplace is a productive one. IoT enhances worker safety by monitoring environmental conditions and equipment status.
- Sensors can detect gas leaks or hazardous conditions
- Wearable IoT devices track workers' vital signs in real-time
- AI-powered systems alert supervisors in case of emergencies
By proactively addressing safety concerns, manufacturers protect their employees while improving workplace efficiency.
6. Supply Chain Optimization: Enhancing Operational Visibility
Manufacturing doesn’t operate in isolation; it’s part of a broader supply chain ecosystem. IoT provides end-to-end real-time tracking, ensuring transparency from raw material suppliers to end consumers.
Benefits of IoT in supply chains include:
- Reducing delays by optimizing delivery routes
- Minimizing waste through precise inventory tracking
- Ensuring compliance with quality and safety standards
For example, an IoT-enabled logistics system can predict shipment delays and automatically adjust supply chain operations, ensuring uninterrupted production.
7. Real-World Success Stories
Several companies have already leveraged IoT to transform their manufacturing processes:
- Automotive Industry: A major car manufacturer implemented IoT-driven predictive maintenance, leading to a 25% reduction in unexpected equipment failures.
- Electronics Industry: A consumer electronics company used IoT for inventory management, cutting holding costs by 20% and improving order fulfillment.
These real-world applications highlight how IoT is reshaping manufacturing, improving efficiency, and reducing operational costs.
8. Embracing the IoT Revolution
Adopting IoT in manufacturing isn’t just about installing sensors; it’s about embracing a culture of continuous improvement and innovation. It involves:
- Investing in the right technology
- Training staff to use IoT-driven insights
- Partnering with experts to develop tailored solutions
The journey may seem daunting, but the rewards—increased efficiency, cost savings, and enhanced competitiveness—are well worth the effort.
Conclusion
The integration of IoT in manufacturing is more than a trend; it’s a transformative approach reshaping the industry. From predictive maintenance to energy management, IoT applications are driving efficiencies that were once unimaginable.
As manufacturers navigate this digital landscape, collaborating with experts in custom software development services can provide the tailored solutions needed to harness IoT’s full potential. The future is here, and it’s interconnected. Are you ready to join the revolution?
FAQs
IoT (Internet of Things) in manufacturing refers to the use of connected sensors, devices, and smart systems to collect and analyze real-time data, improving efficiency, automation, and decision-making in production processes.
IoT enhances efficiency by enabling predictive maintenance, optimizing energy consumption, improving quality control, automating inventory management, and streamlining supply chain operations.
The main challenges include:
- High initial investment in technology and infrastructure
- Cybersecurity concerns related to data breaches
- Integration complexities with existing legacy systems
- Training workforce to leverage IoT effectively
Yes, IoT reduces production costs by minimizing equipment downtime, reducing energy waste, preventing overstocking or stock shortages, and automating repetitive tasks to reduce labor costs.
IoT sensors monitor equipment health in real-time, detecting irregularities like temperature fluctuations, vibration changes, or excessive wear. This allows manufacturers to address potential failures before they happen, reducing downtime and maintenance costs.
Share this post
Leave a comment
All comments are moderated. Spammy and bot submitted comments are deleted. Please submit the comments that are helpful to others, and we'll approve your comments. A comment that includes outbound link will only be approved if the content is relevant to the topic, and has some value to our readers.
Comments (0)
No comment