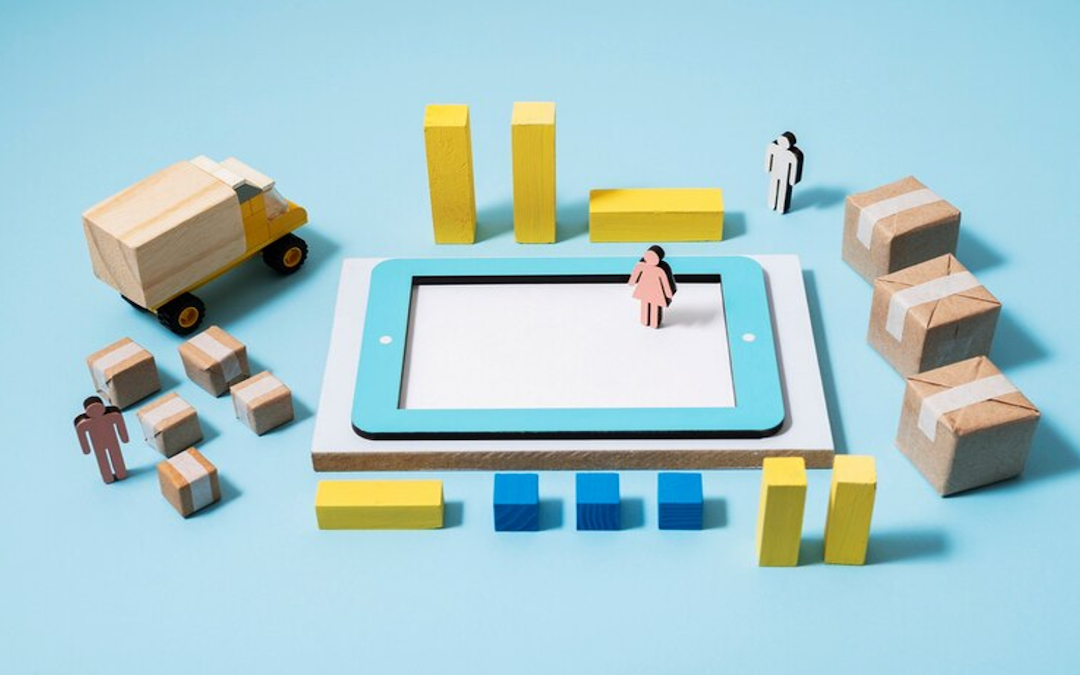
Inventory management is a very important aspect of the management of any business that deals with tangible goods. Inventory control enables one to track the status of their stock in real-time, reduce wastage, enhance their cash flow, and be in a position to make the right choices on what to order and when.
It is crucial for business owners and managers to know how to create an inventory system. As for large enterprises, complex systems are available and for small businesses, it is possible to at least have a simple inventory tracking process implemented by using spreadsheet software and barcoding technology.
Learning how to design an inventory management system tailored to your specific needs can significantly improve your operational efficiency and bottom line. For those seeking more advanced solutions, inventory software development services can create custom systems tailored to specific business needs.
Determine Your Inventory Management Goals
When considering how to build an inventory management system, it's crucial to start by outlining your objectives for inventory control based on the specific needs and operations of your business. This is the first step that will help you in decision-making when choosing the right system or when designing one.
Key goals may include:
- Cutting operating expenses that are incurred as a result of holding more inventory than is needed.
- Out-of-stock should not happen and this can be prevented by tracking the usage and lead time.
- Determination of slow and fast-moving products.
- Simplifying the order placement as well as reordering of products.
- Offering a current status of products as they are sold in the market by giving real-time updates.
- Having a method of tracking the value of inventories for reporting purposes.
- Optimizing the process of order handling and delivery.
- Improving, for example, the location and density of storage space in a warehouse.
If operating an online store or in multiple outlets, a goal may also be to establish a central inventory management system throughout your distribution channels.
Choose Your Inventory Management Platform
With your goals in mind, you can now select an appropriate inventory management platform. Understanding how to make an inventory system is crucial for effectively managing your stock.
Some popular options include:
Spreadsheets
Microsoft Excel or Google Sheets are affordable and flexible tools for storing inventory data. They offer functions like formulas for calculations, conditional formatting to highlight issues, and data visualization through charts or pivot tables. Additionally, cloud-based spreadsheets enable real-time information sharing across multiple devices, making inventory management more collaborative and efficient.
Barcode Scanners
When paired with spreadsheets, affordable barcode scanners help achieve fast and accurate tracking by eliminating manual data entry. Barcode labels can be applied to products and locations, syncing seamlessly with the spreadsheet system. For added convenience, mobile devices like phones or tablets can also be used to scan barcodes.
Software Apps
Dedicated inventory management software offers enhanced functionality over spreadsheets for more advanced users. Common features include barcode labeling and scanning, digital workflows, role-based access controls, and integration with eCommerce platforms or accounting software.
Cloud-based apps provide access to data anytime and anywhere and often include POS integration. However, they require monthly subscription fees, and costs can increase as more inventory or locations are added.
Set Up Your Inventory Spreadsheet
For small businesses wondering how to start an inventory system, a simple yet effective approach is to use Excel or Google Sheets as the foundation. This method provides an accessible way to begin managing your inventory without investing in complex software. To start an inventory system using this approach, set up the following tabs in your spreadsheet to structure your tracking process:
Key Inventory Spreadsheet Tabs
- Products. Master list of all items, with unique ID/SKU numbers, descriptions, pricing, etc.
- Locations. List of warehouses, retail stores, vehicles from which inventory is fulfilled.
- Inventory levels. Current snapshot of product quantities by location.
- Stock movements. Log of all goods received and goods issued transactions.
- Reorder points. Defines par stock levels to trigger reordering for each product.
- Purchase orders. Tracks details of incoming orders to vendors.
- Suppliers. Database of vendor contacts and account details.
Implement Barcode Tracking
To maximize efficiency and reporting accuracy in how to make an inventory system, introduce barcode tracking for all inventory transactions including:
- Receiving stock from suppliers.
- Putaway to storage locations.
- Picking/transferring to other locations.
- Shipments to customers.
- Cycle counts.
When learning how to set up an inventory system, download affordable barcode software to design and print number sequences on standard label sheets. Apply barcode stickers to products, racks, bins, and shelves. Then simply scan codes during any inventory moves rather than error-prone manual data entry.
A key aspect of creating an inventory system is using mobile devices, handheld scanners, and barcode guns, which offer portability to also capture inventory during physical counts. Transactions sync back to the central spreadsheet in real time, completing your efficient inventory system.
Define Your Reorder Points
A vital component is establishing reorder points for each product – the specific quantity thresholds that automatically trigger when it's time to replenish your stock.
Accounting for average lead times from suppliers plus expected demand before new orders arrive, the reorder point formula is:
Reorder Point = (Average Lead Time in Days x Average Daily Usage) + Safety Stock
Build this formula into your Products tab, allowing minimums and other inputs to be adjusted. Conditional formatting visually indicates when any items have fallen below target levels.
Maintain Accurate On-Hand Balances
The true test of any inventory system is whether the on-hand quantities it reports match what is physically available in your warehouse or stores. When discrepancies occur, sales and customer satisfaction are impacted.
Follow best practices around recording inventory transactions like receipts and shipments in real-time, performing routine cycle counts, and accounting for any inventory adjustments.
Conclusion
To any business dealing with stocks especially those that deal with physical products, it is crucial to have an efficient inventory management system. Thus, with the help of such tools as spreadsheets and barcodes, small businesses can introduce affordable and easily scalable tracking to gain real-time control over stock and make sound decisions in terms of inventory management over time.
Share this post
Leave a comment
All comments are moderated. Spammy and bot submitted comments are deleted. Please submit the comments that are helpful to others, and we'll approve your comments. A comment that includes outbound link will only be approved if the content is relevant to the topic, and has some value to our readers.
Comments (0)
No comment