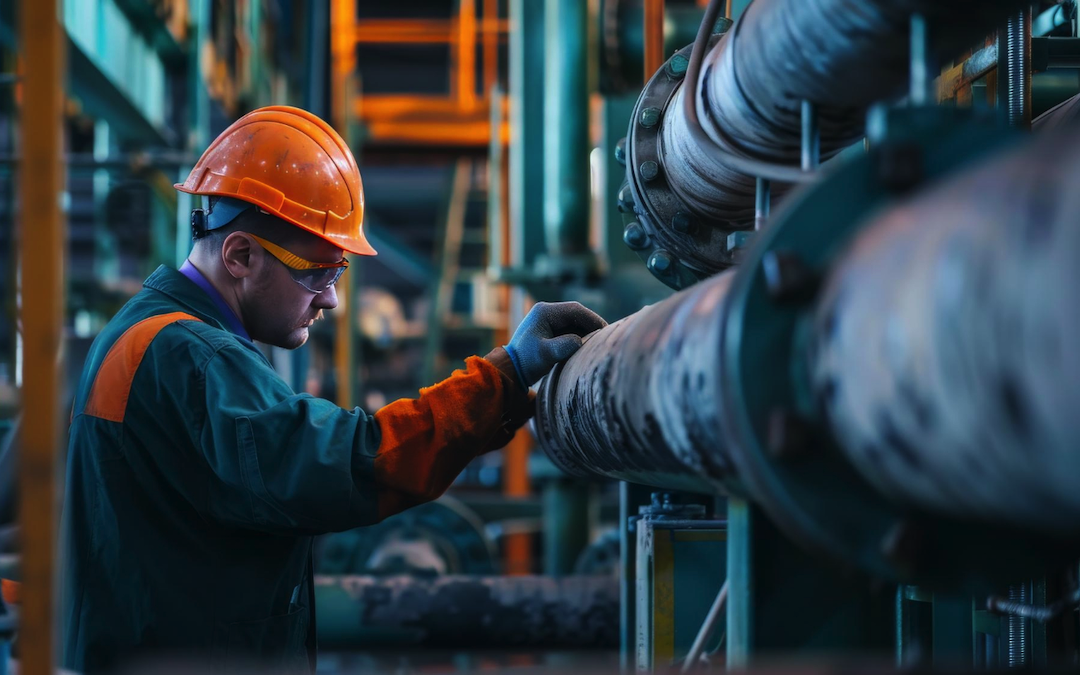
Acoustic leak detection has become an important tool for industries that do not want equipment failures, environmental pollution, or other negative consequences. With new technology like acoustic imaging cameras, finding leaks is faster and more accurate, allowing companies to spot issues right when they start.
Therefore, this real-time detection means companies can quickly schedule repairs and prevent unexpected equipment breakdowns, which helps avoid expensive downtime. Furthermore, using these detection methods helps industries reduce interruptions, limit serious damage, and create a safer workplace for employees.
This article explains five popular acoustic leak detection methods to help industries strengthen their maintenance strategies.
1. Acoustic Imaging Cameras
Acoustic imaging cameras use advanced microphones to detect the ultrasonic sound waves of every leak in pressurized systems. These devices offer exact localizations for acoustic leak detection, usually locating a leak within a few centimeters.
For example, acoustic imaging cameras are installed with up to 200 microphones, which capture real-time sound frequencies to detect gas leaks, electrical discharges, and mechanical breakdowns faster.
Even small leaks let loose ultrasonic sound waves when gas or fluid escapes, which these cameras interpret onto a visible screen. Visual information on a screen identifies the immediately located leak source.
It measures the magnitude of the leak, among other things, and has to make thorough, proximal inspections, which can be dangerous. Besides, the cameras can detect leaks as much as 10 times faster than other traditional methods.
In addition to efficacy and efficiency, they are highly versatile because they can be used in gas leak detection, fluid leak detection, and partial electrical discharge detection.
2. Ultrasonic Detectors
Ultrasonic leak detectors are small, lightweight, hand-held instruments intended to detect high-frequency sounds that indicate the presence of leaks.
They work particularly well in environments where ambient noise might otherwise mask the sound of a leak since the ultrasonic signals are converted to audible tones that technicians can easily interpret.
Also, these detectors operate on scanning frequencies above the human hearing range, normally above 20 kHz. They are tuners oriented toward picking up ultrasonic emissions produced by pressurized leaks and are reliable means of locating problems quickly.
In addition, ultrasonic detectors detect air and gas leaks in moderately pressurized systems. Their operation is relatively simple, requiring little to no training, and portable, enabling technicians to perform a rapid assessment at many locations within the facility.
3. Vibration Analysis
Vibration analysis, while traditionally used to monitor machinery health, can also help detect leaks indirectly by identifying unusual vibration patterns. When a leak occurs, it often creates irregular vibrations in equipment or pipelines due to changes in pressure and the movement of escaping fluids or gases, which can indicate a potential leak.
Therefore, vibration sensors are attached to machinery to monitor for any continuous unusual frequency changes. A leak disrupts normal pressure levels, altering the equipment's vibration patterns and signaling a possible leak or mechanical issue.
This approach enables early leak detection by identifying shifts in normal operational patterns and supports predictive maintenance by tracking these patterns over time. It's widely used across industries like manufacturing and energy, where it not only aids in leak detection but also helps prevent breakdowns by identifying issues before they become critical.
4. Geophones
Geophones are sensitive ground-to-contact microphones that detect leaks in underground pipes and tanks. In nature, sophisticated tools capture the peculiar sound waves and vibrations emanating from fluid escaping through cracks or holes in buried infrastructures.
The passing of liquids through these openings constitutes a variety of acoustic signals traveling into the surrounding soil. Apart from this, modern geophones use advanced filtering technology to distinguish leak sounds from background noise; thus, their effectiveness is remarkable even in busy urban environments.
These device sensors, normally laid down at strategic intervals along the suspected leak path, are capable of transmitting the location of the problem through the measurement of the intensity and characteristics of such acoustic signals.
Therefore, the maintenance teams can precisely direct their efforts to repair in exemption of unnecessary excavation, thus saving them a lot of time and resources.
5. Soap Bubble Method
The soap bubble method is a simple, low-cost procedure to confirm a suspected leakage location after other methods have detected leakage. A soap or detergent solution has an area sprayed where leakage is suspected.
If gas escapes, bubbles will appear while it discharges through the solution, visually confirming the exact spot of the leak. This method is often a final verification step with acoustic or ultrasonic detection tools.
Also, the soap bubble technique is inexpensive and easy to conduct, assuming the simplest tools. It suits finding tiny low-pressure leaks, which other methods can hardly decode precisely.
However, this is limited to nonhazardous and accessible places because it can detect only surface-level leaks in spots that technicians can easily reach. Thus, although it provides visible confirmation, it is normally used as a supplemental tool in leak detection practices.
Final Thought
Acoustic leak detection is vital in maintaining industrial safety and operational efficiency.
This innovative technology helps identify leaks swiftly and accurately, preventing potential hazards and costly equipment failures.
By implementing a comprehensive approach combining sophisticated and straightforward detection methods, facilities can effectively monitor their systems for any signs of leakage.
Comments (0)
No comment