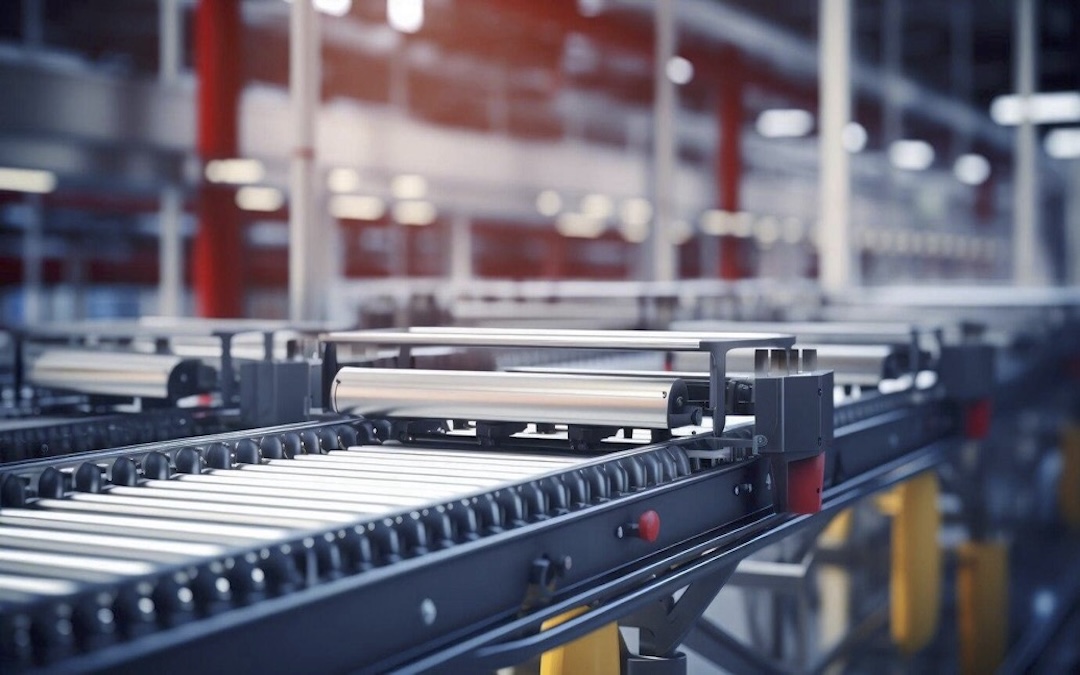
Efficiency remains a top priority for many manufacturing businesses. With competitive pressures on cost reductions, productivity improvements, and high-quality standards, businesses find themselves between a rock and a hard place. Businesses today look at advanced machinery solutions that will lighten this process for them. Automation, precision equipment, and material handling systems-these machines alone can help magnify efficiency in the processes of manufacture manyfold.
In this article, some of the most effective manufacturing process equipment and solutions will be considered to ensure optimization in manufacturing operations for long-term success.
Automation Systems for Streamlining Production
The most effective way of realizing such efficiency in manufacturing is by incorporating automation systems into your production line. Automation applies the use of manufacturing equipment: machines, robots, and control systems to carry out various tasks with minimal human involvement. This will not only increase production speeds but also reduce human errors that lead to costly mistakes and delays.
- Benefits: Increased speed of production, reduced labor costs, less error, and more uniformity.
- Applications: Automation finds its application in assembly lines, packaging, quality inspection, and even material handling. Industries related to automotive, electronics, and food processing benefit a great deal from automation systems.
Let’s look at some industrial equipment examples.
Example Solution: Industrial Robots
Industrial robots are usually applied for assembly, welding, and painting, among many other tasks related to production. Working for 24/7 with high precision largely enhances throughput and consistency in products. Modern robots, with advanced AI, adapt easily to changes in production and, therefore, are quite flexible and efficient.
CNC Machines for Precision Manufacturing
Computer Numerical Control machines have been the backbone of present-day manufacturing, characterized by high accuracy and repeatability. Computers control CNC machines to conduct complicated machining tasks, including cutting, milling, drilling, and turning, with incredible accuracy. This form of accuracy is indispensable in making complicated parts with close tolerances.
- Benefits: High precision, very repeatable, and enables the creation of complex designs.
- Applications: These manufacturing equipment find their application in industries ranging from aerospace, automotive, medical devices, to consumer electronics – manufacturing everything from engine components and medical instruments to circuit boards.
Example Solution: CNC Milling Machines
CNC milling machines are capable of a number of functions, which range from drilling to the shaping of metals and plastics. It finds broad applications in industries requiring parts in very irregular shapes with great detail. These machines are versatile and very accurate; thus, allowing manufacturers to meet their customer demands for stringent specifications.
Material Handling Systems for Efficient Logistics
Effective material handling plays a great role in the smooth and continuous operations of any industrial equipment manufacturing facility. Material handling systems include conveyors, automatic guided vehicles, and palletizers, among others that help in moving raw materials, components, and finished products along the production chain with little human intervention. Such systems reduce manual labor and improve safety, hence assuring continuous and well-organized material flow.
- Benefits: Increased efficiency, reduced labor costs, enhanced safety, and optimized material flow.
- Applications: Material handling solutions are used in industries like automotive manufacturing, food processing, logistics, and warehousing.
Example Solution: Conveyor Systems
Conveyor belts find a wide application in industrial equipment manufacturing because they deal with the transportation of materials or products from one station to another. An automated conveyor system reduces the downtime of a manufacturer while continuing the production flow. Such systems are designed for various production lines in order to improve productivity by reducing human labor.
Electric Motors – The Backbone of Modern Manufacturing Operations
With the energy-efficient, less noisy, and longer useful life, the advantages of electric motors have made them a darling of modern manufacturing. Besides their precision and the ability to give accurate speed and torque, the motor applies in performance that calls for consistent results and dependability. More importantly, electric motors have lower maintenance requirements compared to other mechanical systems, hence lower downtime and operational costs.
Electric motors find broad applications in industries ranging from automotive and robotics to consumer electronics and industrial automation. From the manufacturing point of view, electric motors drive the assembly lines, conveyor belts, tools such as CNC machines, and robotic arms. They are indispensable in applications requiring high precision, constant speed, and high torque, such as in electric vehicles, home appliances, and HVAC systems.
Example Solution: Servo Motors
Servo motors are a class of electric motors used for precision in angular or linear position, velocity, and acceleration. Applications that these motors are expected to serve include those requiring high accuracy and performance. Servo motors have wide applications in robotics, CNC machinery, and packaging systems. Servo motors demonstrate great efficiency and may act at variable speeds; as a result, they serve well in modern manufacturing applications where flexibility and precision may both be required.
Advanced Quality Control and Inspection Systems
Quality control has turned out to be a very demanding activity in the present industrial equipment manufacturing scenario. Advanced inspection systems, such as vision systems, coordinate measuring machines, and laser scanners, enable the examination of parts and products with respect to defects, precision, and consistency in dimension. Accordingly, automation in quality control helps reduce human errors to almost zero, hence upgrading product quality to allow only the best ones to hit the market.
- Benefits: Enhanced product quality, reduced waste, faster inspections, and improved consistency.
- Applications: Used in automotive, electronics, medical device manufacturing, and aerospace industries, where precision and quality are critical.
Example Solution: Vision Inspection Systems
Typically, vision inspection systems use cameras and AI software in product flaw detection while the latter are moving along the line. Applications range from surface imperfection analysis and dimensional measurements to functional quality testing of assemblies, including immediate feedback to the operators by assuring that only perfect goods reach the customers.
Pumps – Essential Components for Fluid Handling in Manufacturing
Pumps are highly important in many manufacturing processes, as they deliver the transportation of fluids, gases, or slurries within systems. They can be used in everything from cooling systems and lubrication circuits to chemical processing and water treatment plants, moving liquids and gases around. Pumps are available in various types and sizes for versatility and efficiency in a great many different manufacturing applications.
Pumps boost very high efficiency in the process of fluid or gas transferring with minimum consumption of energy; hence, they are cost-effective and highly dependable to maintain proper production flow. They give full control over the fluid transfer, are durable, and hence can perform under tough working conditions. Besides this, pumps decrease downtime and lower maintenance costs by making their operation consistent and lowering the chances of leakage or malfunction.
They are used in such areas as chemical processing, automotive industries, food and beverage handling, pharmaceutical industries, oil and gas industries. In manufacturing, pumps have huge importance in raw material transfer, coolant circulation, lubrication, and wastewater handling. They also find application in operations requiring fluid-based processes to possess consistent and accurate flow control.
Example Solution: Centrifugal Pumps
Centrifugal pumps are among the most common in manufacturing due to their capability to handle a wide range of fluids, from water and oils to chemicals. They transfer fluids by means of rotational energy; thus, they offer a continuous and smooth flow. They are ideal for applications such as coolant circulation in CNC machines, liquid transfer in chemical processing, and fluid pumping in water treatment systems. Centrifugal pumps are highly valued because of their efficiency, reliability, and the capability of handling variable flow rates and pressures.
Final Thoughts
From general machinery, solutions, and tooling for improving productions that enable more efficient, effective, and cost-effective services, smooth manufacturing operations depend on everything. The modern manufacturer utilizes Automation Systems, CNC Machines, Material Handling Solutions, 3D Printing, and Advanced Inspection Systems very viable tools for modern competitive requirements in today's marketplace. These will enable the manufacturer to cut inefficiency, and quality variation of the product, and hit their bottom line by integrating these advanced machinery solutions into their operations. Indeed, investment in the right machinery is the key to success in today's fast world of manufacturing.
Related Posts
Share this post
Leave a comment
All comments are moderated. Spammy and bot submitted comments are deleted. Please submit the comments that are helpful to others, and we'll approve your comments. A comment that includes outbound link will only be approved if the content is relevant to the topic, and has some value to our readers.
Comments (0)
No comment